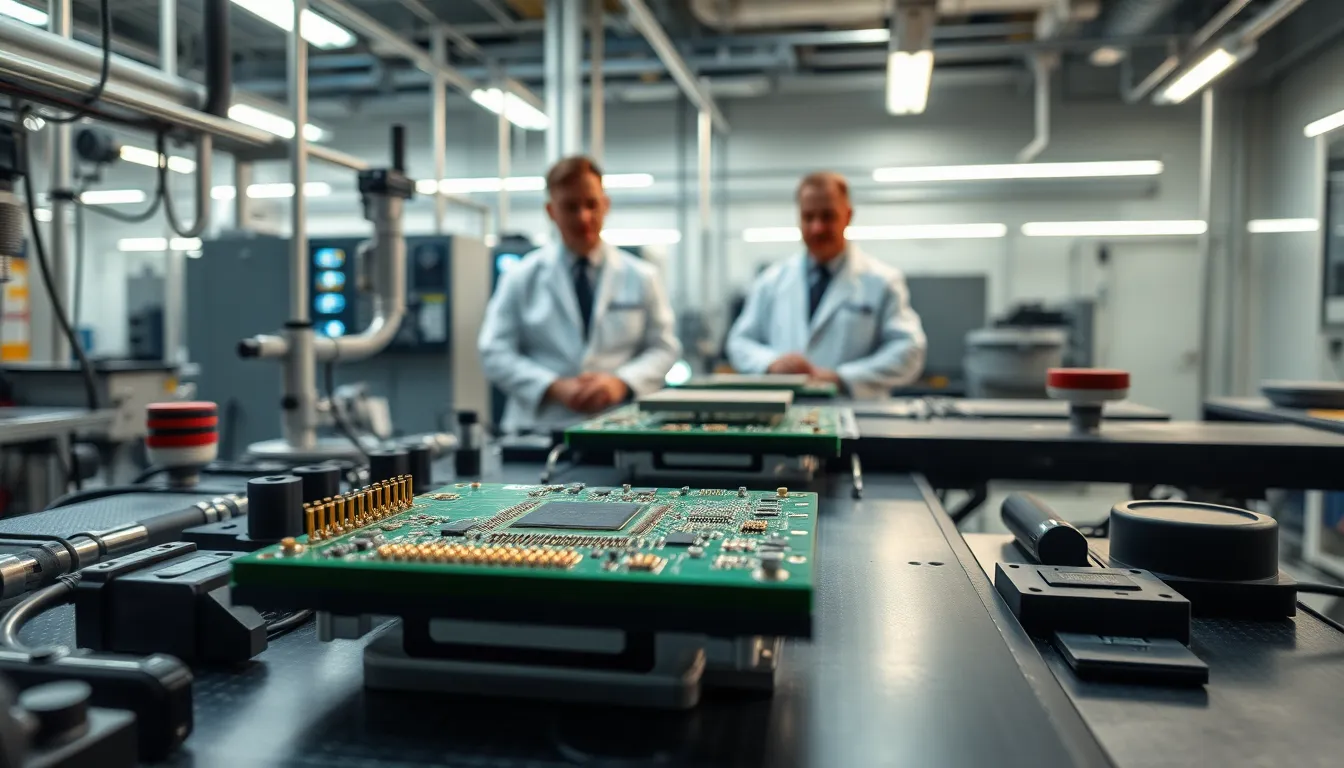
Key Takeaways
- High frequency PCBs are essential for advanced electronic applications, supporting fast, reliable signal transmission in industries like telecommunications, aerospace, and automotive.
- Selecting a top manufacturer requires evaluating expertise in high-frequency materials (such as PTFE, Rogers, and Taconic) and strict quality certifications like ISO 9001 and IPC standards.
- Leading manufacturers like WellPCB, Rush PCB, and RayMing Technology offer advanced capabilities, including automated production, precision process control, and rapid prototyping for frequencies up to 100 GHz.
- Key factors in choosing the right supplier include material compatibility, fabrication capabilities, global certifications, design support, and responsive customer service.
- Ensuring strong quality control and technical support from your high frequency PCB manufacturer directly impacts product performance, reliability, and market competitiveness.
High frequency PCBs are essential for advanced electronics applications, ensuring fast and reliable signal transmission in telecommunications, aerospace, and automotive industries. These specialised circuit boards operate above 500 MHz and require manufacturers with expertise in advanced materials like PTFE and Rogers substrates. Selecting the right high frequency PCB manufacturer directly impacts product performance and longevity. Leading providers such as WellPCB offer cutting-edge technology and expert engineering support to help companies maintain competitive advantages in demanding markets.
What Is a High Frequency PCB?
A high frequency PCB supports signal transmission at frequencies above 500 MHz, with many designs in applications like RF, microwave, and 5G wireless operating between 1 GHz and 60 GHz. These boards use special substrate materials like PTFE, Rogers, or hydrocarbon ceramic laminates, while standard FR-4 material creates too much signal loss at higher frequencies. Materials that minimize dielectric constant (Dk) variation and ensure low dissipation factor (Df) improve high-frequency performance and reduce signal integrity issues.
Designers use high frequency PCBs when they need fast signal speeds and minimal attenuation, such as radar, satellite, GPS, base stations, or automotive collision avoidance. Manufacturers like WellPCB in China use automated manufacturing lines and advanced material sourcing to meet stringent requirements for thickness tolerance, copper surface quality, and controlled impedance structures. WellPCB also provides quick turn prototyping for RF and microwave engineers and offers design consultation to address Dk, Df, and impedance requirements common in high frequency circuits. High frequency PCB solutions improve reliability and stability in advanced electronic products used worldwide.
Key Criteria for Selecting a High Frequency PCB Manufacturer
Selecting a top high frequency PCB manufacturer depends on strict evaluation of core technical criteria. High-performance applications in telecom, aerospace, and automotive demand boards with precise material, process, and support standards to ensure reliable signal integrity.
Quality and Material Standards
Reliable high frequency PCB manufacturers use materials with low dielectric constant (Dk) and low loss tangent (Df) to maintain signal clarity at GHz frequencies. Rogers 4003, Rogers 4350, Taconic TLY, and PTFE-based laminates are common choices for these boards because they reduce signal loss and distortion. Manufacturers like WellPCB source tested high-frequency substrates and verify sheet quality before production. Material control prevents unexpected impedance changes, which is vital for frequency ranges above 1 GHz. Adherence to international quality benchmarks for PCB laminates secures stable electrical characteristics across batch productions.
Manufacturing Capabilities and Equipment
Advanced manufacturing capabilities are needed for consistent high frequency PCB production. Precision equipment must support controlled impedance traces, tight thickness tolerances, and multilayer stack-ups without defects. WellPCB operates with fully automated drilling, lamination, and plating lines to deliver consistent results for designs up to 60 GHz. Equipment calibration is routine to eliminate alignment shifts that could degrade signals in radar, satellite, or automotive applications. Each manufacturing step uses statistical process control to catch errors before they affect finished products, so boards stay within strict electrical and physical tolerances.
Certifications and Compliance
Certifications such as ISO 9001 and IPC standards are baseline requirements for top high frequency PCB manufacturers. Environmental regulations like RoHS compliance further ensure products meet global safety and reliability expectations. WellPCB holds ISO 9001 and implements traceability systems on all production lots to document quality control. These certifications validate that production processes meet strict industry standards, giving customers confidence in PCBs for critical communication, defense, or medical systems. Ongoing updates to certification processes follow changes in regulatory requirements and best practices for PCB manufacturing.
Customer Support and Service
Available customer support is a key differentiator among high frequency PCB manufacturers. Leading suppliers provide engineering consultation on stack-up, substrate, and impedance options at the design stage, reducing prototype revisions and time-to-market. WellPCB’s technical support team helps customers interpret fabrication notes and optimize layouts for yield and performance. Prototyping services enable rapid evaluation and troubleshooting, which is critical for time-sensitive projects in sectors like automotive radar or wireless infrastructure. Accurate feedback from support teams can prevent costly mistakes and keep projects aligned with demanding specifications.
Top High Frequency PCB Manufacturer: Detailed Reviews
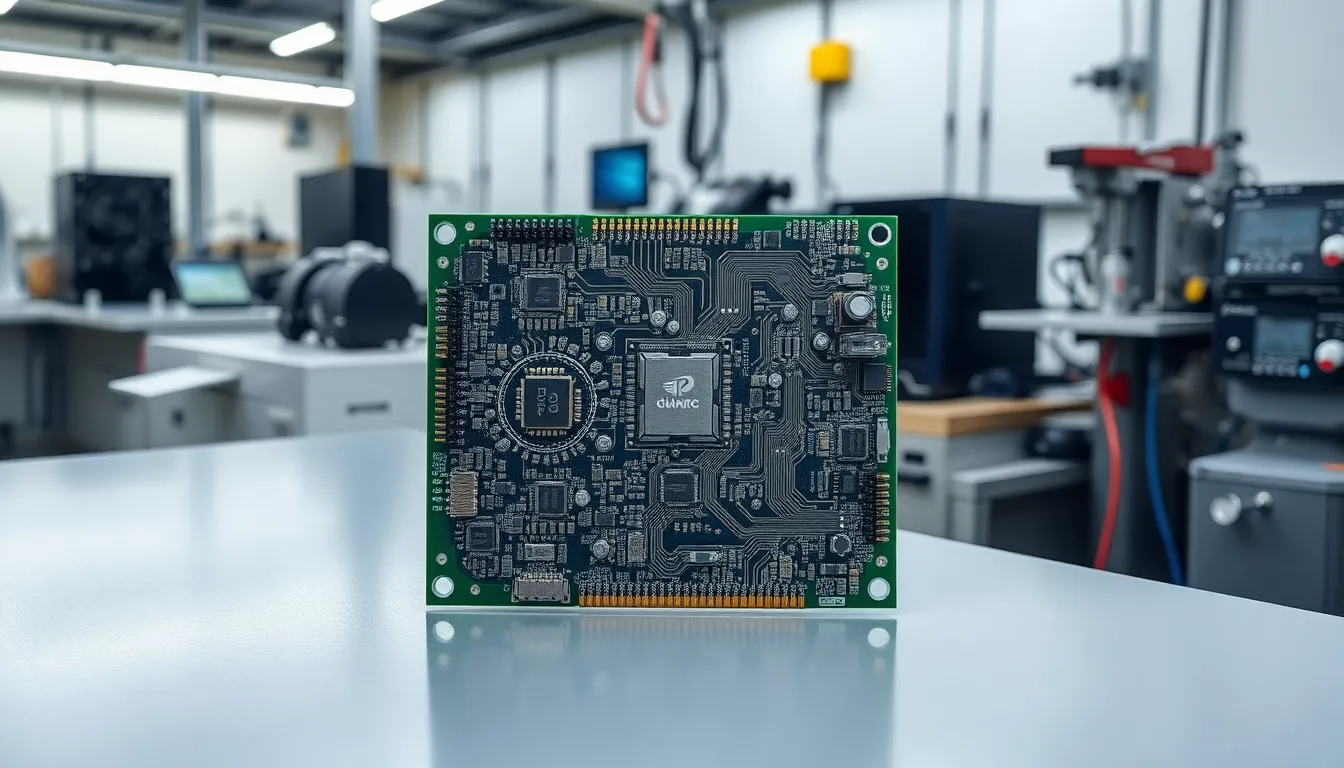
Top high frequency PCB manufacturers deliver advanced board solutions for demanding sectors like RF communications, satellite, and automotive radar. Each leading supplier relies on precision processing and specialized materials to handle GHz-range applications with strict signal integrity requirements.
Manufacturer 1: Rush PCB
Rush PCB operates in the USA and China, producing high frequency PCBs up to 100 GHz. Facilities support rigid, rigid-flex, and Kapton PCBs using high-speed substrates with low Dk/Df values. The company enables trace widths down to 2 mil for compact routing, multi-layer lamination from 1 to 40 layers, and integrates AOI and TDR testing for quality assurance. Laser routing and advanced lamination processes enable products for aerospace, automotive radar, and communications equipment. Rush PCB’s engineered boards use tailored dielectric materials for markets where rapid signal propagation and controlled impedance drive end-product reliability.
Manufacturer 2: RayMing Technology
RayMing Technology manufactures high frequency PCBs from China for RF, wireless, and microwave products. Capabilities target frequencies above 25 GHz, processing Rogers, Taconic, and Arlon high-frequency laminates for minimal signal attenuation. Laser drilling, rigid-flex assembly, and advanced process controls enable production for telecommunication, radar, and satellite end uses. RayMing’s facilities support multi-layer designs for industrial, defense, and IoT infrastructure. Products feature consistent impedance and use of materials designed for low loss at critical GHz frequencies where signal reliability and stability are essential.
Manufacturer 3: WellPCB
WellPCB, based in China, supplies high frequency PCBs using tested substrates like PTFE and Rogers for applications up to 60 GHz. Production lines incorporate automated inspection and solder mask control for signal reliability in GPS, automotive, and satellite systems. WellPCB offers rapid prototyping, impedance control, and volume production for global customers in communications and radar markets. Certifications including ISO 9001 and IPC standards ensure board quality. Experienced engineers support design for manufacturability and compliance, helping ensure project timelines and performance standards are met for electronic developers worldwide.
Comparing the Top High Frequency PCB Manufacturers
The top high frequency PCB manufacturers excel by using advanced material systems, precision processes, and strict quality controls to support signals above 25 GHz. WellPCB in China delivers PCBs operating up to 60 GHz, combining fine trace capabilities with certified automated manufacturing and comprehensive testing systems.
AT&S in Austria supports frequencies over 100 GHz, using PTFE and ceramic for demanding telecom and radar sectors. TTM Technologies in the USA handles designs up to 80 GHz, leveraging PTFE composites and ceramics for HDI, microvias, and reliable rigid-flex solutions.
RayMing Technology in China offers PCBs above 25 GHz with Rogers, Taconic, and Arlon substrates. This approach supports laser drilling and advanced trace geometries for compact, high-speed assemblies. In Taiwan, Compeq and Elec & Eltek both target automotive radar and industrial uses, utilizing Rogers 4000 laminates for stable performance up to the 76–77 GHz range.
San Francisco Circuits in the USA focuses on modeling and analysis for PCBs up to 90 GHz, supporting aerospace and mmWave applications. These manufacturers commonly use PTFE, Rogers, Taconic, and ceramic, as these materials ensure reliable signal integrity critical to high-frequency deployments.
WellPCB enhances product reliability with quick prototyping, traceability, and compliance with ISO and IPC standards, giving users consistent quality for 5G, radar, satellite, and IoT projects.
How to Choose the Best Manufacturer for Your Needs
Choosing the best high frequency PCB manufacturer relies on matching project requirements with the provider’s technical strengths and certifications. Key decision factors include frequency range, material compatibility, fabrication tolerances, and quality standards.
- Match Technical Specifications: Select manufacturers that support the required frequency—such as WellPCB for up to 60 GHz and PTFE, Rogers, or other low-loss substrates. Confirm support for rigid, flexible, or rigid-flex types and precise layer counts.
- Assess Fabrication Capabilities: Identify providers offering fine line resolution, microvias, and backdrilling, which are essential for dense designs. WellPCB uses automated inspection and tight process controls, addressing small trace spacing and impedance targets.
- Prioritize Certified Quality: Require ISO 9001 and IPC compliance for international reliability. Industries like automotive or medical should check for IATF 16949 or ISO 13485, which global companies like WellPCB or TTM Technologies maintain.
- Verify Rapid Prototyping and Design Support: Choose firms that deliver prototypes fast—WellPCB offers quick-turn capabilities with design consultation to minimize errors and speed product iterations.
- Check Communication and Service: Ensure local support or 24/7 assistance for engineering queries and after-sales service. WellPCB provides remote access, engineering guidance, and traceable batch management to streamline the process for global clients.
- Balance Cost and Lead Time: Evaluate the cost-to-quality ratio and flexibility in urgent or low-quantity PCB runs. Transparent pricing and confirmed lead times, as offered by WellPCB, support efficient production scheduling worldwide.
About WellPCB
WellPCB is a leading provider of PCB manufacturing and assembly services, offering a full range of solutions to meet the needs of various industries.
Co-founded by Hommer Zhao, who also serves as the Director of Sales and Marketing, WellPCB provides services including PCB prototyping, turnkey PCB assembly, and rapid prototyping. With locations in Los Angeles, USA, Cavite, Philippines, and Shijiazhuang, China, WellPCB delivers high-quality, precision-engineered PCBs tailored to client specifications. Their team is committed to providing efficient, cost-effective, and high-performance PCB solutions to support industries like electronics, telecommunications, and automotive.
Contact:
Hommer Zhao, Director of Sales and Marketing, Co-founder
Phone: (424) 842-2783
Email: [email protected]
Website: www.wellpcb.com
Frequently Asked Questions
What is a high frequency PCB?
A high frequency PCB is a printed circuit board designed for signal transmission at frequencies above 500 MHz, often used in applications like radar, satellite, telecommunications, and automotive systems. These boards rely on specialized materials to ensure fast, reliable, and low-loss signal transmission.
Why are specialized materials important in high frequency PCBs?
Specialized materials such as PTFE, Rogers, or ceramic laminates are crucial because they have a low dielectric constant (Dk) and low loss tangent (Df), which help minimize signal loss and maintain signal clarity at high frequencies, unlike standard FR-4 material.
What industries use high frequency PCBs?
High frequency PCBs are essential in industries such as telecommunications, aerospace, automotive (especially for collision avoidance systems), medical devices, and advanced consumer electronics, where fast and reliable signal transmission is required.
How do I choose the right high frequency PCB manufacturer?
Select a manufacturer based on their experience with high frequency designs, certifications (like ISO 9001 and IPC), advanced materials sourcing, fabrication tolerances, and customer support. Also, consider their prototyping speed and ability to meet your specific frequency and technical requirements.
What certifications should a high frequency PCB manufacturer have?
Look for manufacturers with ISO 9001 and IPC certifications. These standards ensure the manufacturer follows rigorous quality, safety, and reliability procedures essential for critical and high-speed electronic applications.
What is controlled impedance, and why does it matter?
Controlled impedance refers to the precise management of signal transmission characteristics in a PCB trace. It is vital in high frequency PCBs to prevent signal reflection, minimize loss, and maintain signal integrity, especially at GHz frequencies.
Why is prototyping important when developing high frequency PCBs?
Prototyping allows for early testing and validation of PCB designs, helping identify and fix issues before mass production. Quick prototyping from a skilled manufacturer can reduce your time-to-market and improve the reliability of your final product.
Which manufacturers are known for high frequency PCB production?
Leading manufacturers include WellPCB, RayMing Technology, Rush PCB, AT&S, TTM Technologies, and San Francisco Circuits. They are recognized for their ability to produce PCBs that support frequencies above 25 GHz, advanced materials, precision processes, and strict quality control.
What is the typical frequency range that top manufacturers support?
Top high frequency PCB manufacturers support designs ranging from 1 GHz up to over 100 GHz, depending on the application and chosen materials.
How do advanced manufacturing capabilities impact high frequency PCB quality?
Advanced manufacturing, including automated process control and statistical inspection, ensures precision in layer alignment, thickness tolerance, and trace dimensions, which are essential for reliable high frequency performance and consistent product quality.
Why is customer support important when ordering high frequency PCBs?
Strong customer support, including engineering consultation and design review, helps optimize your circuit designs for performance and manufacturability. This guidance ensures your project requirements are met and reduces the risk of errors or delays in production.